Gilbarco: Communication without speed limit at the gas station supplier
Europe-wide service companies of Gilbarco Veeder-Root transmit spare parts orders automatically with i‑effect® to the central warehouse in Salzkotten.
Whoever calls a car his own regularly holds the company's products in his hands, even though he will hardly know its name: Gilbarco Veeder-Root is the world's leading provider of solutions and technologies for the service station industry, manufacturing fuel dispensers, fuel management systems, tank content management solutions and the like. Headquartered in Greensboro, North Carolina, the company promotes universal product lines, global reach and exceptional customer service to its customers. To guarantee this, fast communication between the international locations is required. For this Gilbarco relies on EDI technology from menten.
European headquarters of the company is Basildon, Great Britain, but the central spare parts warehouse for the entire continent is located in Salzkotten, North Rhine-Westphalia, the main production location of the German Gilbarco GmbH. All spare parts for Europe are stored there in order to relieve the service companies on site of the logistically complex warehousing. The spare parts are managed and prepared for dispatch in ERP software based on IBM i developed by Gilbarco itself. Whenever a service station in a European country needs repair, it contacts the local Gilbarco office. This sends the repair order to Salzkotten and orders the necessary spare parts there.
i‑effect® links heterogeneous systems - so data flows unhindered
When a European spare parts service hub was established in 2013, the aim was to transmit procurement requests from the various countries to Salzkotten as quickly as possible. The goal: 24 hours after the customer's request, the service technician of the national company should be at the filling station with the spare part and install it - hardly possible with the traditional ordering method by telephone, e-mail or fax. The various items of an order always had to be entered manually into the ERP software in Salzkotten before the order could even be processed, assembled and dispatched. "That's why we have relied on electronic transmission via EDI right from the start," says Elmar Teipel, ERP organizer at Gilbarco GmbH. "With i‑effect® we link heterogeneous systems so that data can flow unhindered. The solution from menten GmbH convinced us the most, especially when it comes to operation via a modern user interface. Here menten is far ahead of EDI applications comparable with WebControl."
This is how i‑effect® was implemented in Salzkotten with the commissioning of the spare parts hub. As a first step, Gilbarco connected the national companies of the Nordic countries and Scotland to the software. A wide variety of ERP applications are in use there. As soon as a customer order is received in Finland, the ERP system generates a spare parts order and sends it as an XML file to Salzkotten. i‑effect® converts the XML data stream into the DB2 format of the IBM i-based ERP software. The menten GmbH creates these mappings for Gilbarco in outsourcing.
Adaptations for mapping worked out in teamwork
There was a lot to adjust. Elmar Teipel: "A consulting partner like menten was ideal for this because he is familiar with EDI in the IBM i environment, but does not know where in our ERP software which fields are located in which incoming order data must be entered. Both project partners have combined their know-how to ensure that i‑effect®'s ERP system is properly "fed". For example, it becomes more complicated if article numbers in salt cottages follow a different nomenclature than in Sweden, where they start with "140" and have nine digits. For this purpose, conversion tables had to be set up as translation tables, so to speak. The same applies to addresses. Scotland, for example, often has very long address fields with delivery addresses. The project team has created new address tables so that these can be entered correctly in the ERP system.
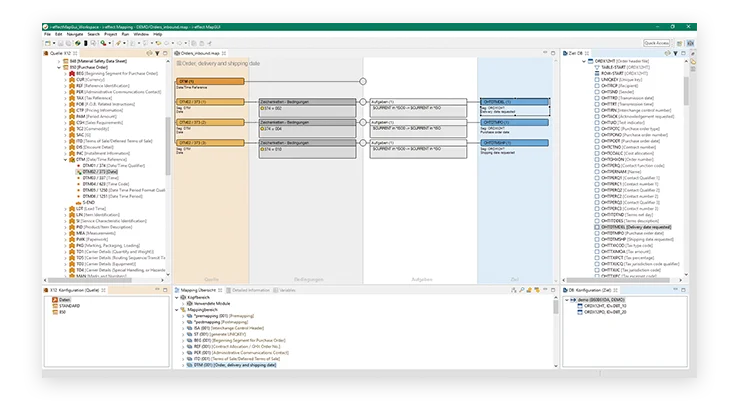
Cleanly functioning communication solution
"Setting up an EDI channel is therefore not a snap of the fingers, but requires proper preparatory work," says Elmar Teipel. "But once it's in place, the communication runs like clockwork. Together with menten GmbH, we have created a cleanly functioning communication solution." This is how it works today: As soon as an order arrives in Salzkotten, i‑effect® automatically sends a status message (Send Receipt) to the sender. In i‑effect®s WebControl (user interface) the user clicks a button "Orders" and has an overview of all incoming orders. At the same time, it is checked in advance whether the stock is available in the warehouse. Some orders are also combined if, for example, orders are received from five different technicians in Finland. The employee on site can sort these orders in WebControl by spare part or also by orderer, summarize them and then let the order flow into the system as a single order.
i‑effect® informs sender about status of spare parts request
If the user opens the ERP mask, he will find all fields prefilled by i‑effect®. Entering a complete job takes an average of three to four seconds. With around 220 jobs per day, this saves just under a quarter of an hour, and yet the processing of each job can start more quickly and, above all, the data is transferred without errors, since typing or slipping in the line is no longer possible. A major advantage of EDI technology is also the greater transparency in the sense that the sender is closely informed about the status of his spare parts enquiry: Once the order has been processed, it receives a second status message (after the send receive), and another shipping message is sent as an advice when it is shipped. Gilbarco also uses i‑effect® for invoicing. Every morning, an automatic mapping job runs that reads the DB2 invoice data from the ERP system, prepares it as an XML file, and sends this invoice message to the recipient. The customer can then compare them immediately with his order.
There are currently four external companies with which Gilbarco communicates in this way. Elmar Teipel does not know whether they are also working in an IBM i environment or whether they are using completely different software systems. He doesn't need to be interested as long as he uses i‑effect® as a mediation and translation instance, which automates the data flow between the different systems. In the medium term, the service companies of other European countries with Salzkotten will also communicate only via EDI. The technical infrastructure is up and running, it is only a question of the respective adaptation work in the mapping area. Bernd Nieder, IT Manager at Gilbarco and responsible for network topics among others, knows that i‑effect® is a flexible solution for this: "We chose menten GmbH because their solution can be adapted exactly to customer needs. The flexibility and functionality and especially the operation via WebControl are unique and also the support of the menten team is fast and competent". A good prerequisite for the further expansion of EDI communication with the No. 1 petrol station supplier.
The company
Gilbarco Veeder-Root develops products for the petrol station industry and is the leading brand for solutions and technologies in the field of fuel management systems, convenience shops, control and environmental effectiveness for fuel distribution and neighbouring markets. The Group has manufacturing, sales, distribution and service facilities in North and South America, Europe, Asia and the Pacific region.
Headquartered in Greensboro, NC, the company has production, research and development centers in Germany, Italy, UK, Denmark, U.S.A., India, Argentina, Brazil, China, Australia and Mexico. The headquarters for Europe, the Middle East and Africa is located in Basildon, Great Britain.
Challenges
The filling station supplier Gilbarco has been operating a European spare parts service hub in Salzkotten since 2013. We were looking for a way to quickly transmit procurement requests from various European service companies to the central warehouse in order to enable rapid delivery of the requested parts.
Solution
i‑effect® receives incoming XML messages from the service companies, converts them into the DB2 format and automatically fills the ERP system in Salzkotten with the order data in the correct fields. WebControl as a graphical user interface, which is oriented towards modern standards of usability, touch technology and intuitive operation, enables intuitive operation of the EDI tool via all common browsers directly on IBMi.
Benefit
i‑effect®'s fast application system is partly responsible for the fact that Gilbarco is able to meet its self-imposed service target today: 24 hours after the customer's request, the service technician of the national company is already at the filling station with the spare part and can install it.