MEYER-HOSEN AG
chooses menten as technology partner
EDI drives digitization in the textile industry
MEYER-HOSEN AG, headquartered in Reichshof-Denklingen, North Rhine-Westphalia, is a leading European specialist for sustainable men's pants. Family-run and regionally rooted in the west of Germany, it operates its own European production center with fair and environmentally friendly framework conditions. The company was named Top Brand 2021 and for its special sustainability by the industry magazine "TextilWirtschaft".
MEYER sells its products to more than 4,000 trading partners in 35 countries worldwide. Data is already exchanged via EDI with almost one fifth of them, and the trend is rising. 30,000 messages per year are received electronically, mostly orders, sales and inventory documents. EDI traffic mainly takes place with these customers; on the supplier side, it plays only a very minor role for various industry-specific reasons.
MEYER-HOSEN AG is constantly striving to improve the technical aspects of EDI traffic with its trading partners - an important element in driving forward digitization within the company. However, this was no longer working well with the original solution: In 2007, the manufacturer had introduced a system that had not been technologically further developed in recent years - for MEYER in 2019, the reason to look for a modern alternative.
Mapping new business models with EDI technology
The company quickly came across menten GmbH as a recognized specialist for EDI and data conversion as well as data integration specifically on IBM i and IBM Power Systems. Geographical closeness also played an important role. "Having a service provider on site is always an advantage, even if many things can already be handled remotely today," says Werner Rampelt, the company's IT manager. The personal contact to the manufacturer and the use of knowledge pools around all EDI topics have been particularly appreciated by the IT as well as the sales team of MEYER over time.
Managing complex projects efficiently
The transition from the old to the new system was silent and took place in close cooperation with IT management, sales and menten GmbH. Nevertheless, a lot of coordination work was of course necessary, because the conversion of established, grown structures with many project participants (ERP supervisors/Infor, internal databases/needs, customer interests and not least the EDI solution as middleware) always means a certain amount of work. Alexandra Pitsch, project supervisor at MEYER comments: "Even though we strive for standard processes and have mostly implemented them, a one-to-one transfer of mappings was not successful in many cases, because customers e.g. have different requirements/fill different fields etc." So standard mappings were developed and these were adapted by menten after individual testing according to customer requirements. For this reason, the data flow had to be monitored particularly intensively in this phase to ensure correct data transfer.
Data maintenance in the own ERP system was also essential. Especially due to the complexity of the EDI migration project, reliable, intuitive tools such as i‑effect®'s WebControl for monitoring and administration of the data streams are indispensable, as is a conscientious integration partner such as menten, which MEYER expressly praises. The conversion was carried out according to urgency and step-by-step according to format types. Master data and Excel lists from the previous tool were programmatically transferred to the new EDI platform i‑effect®. The retail partners were virtually unaware of the migration. Partners in the textile retail trade always have new and often very special requirements for data exchange. This involves transmission paths and rates, new data sets, or formats. "i-effect offers very high flexibility here with its modular system. We can use it to handle different business models via a uniform conversion and communication platform: Connecting online service providers, receiving sales reports, and much more," says Werner Rampelt.
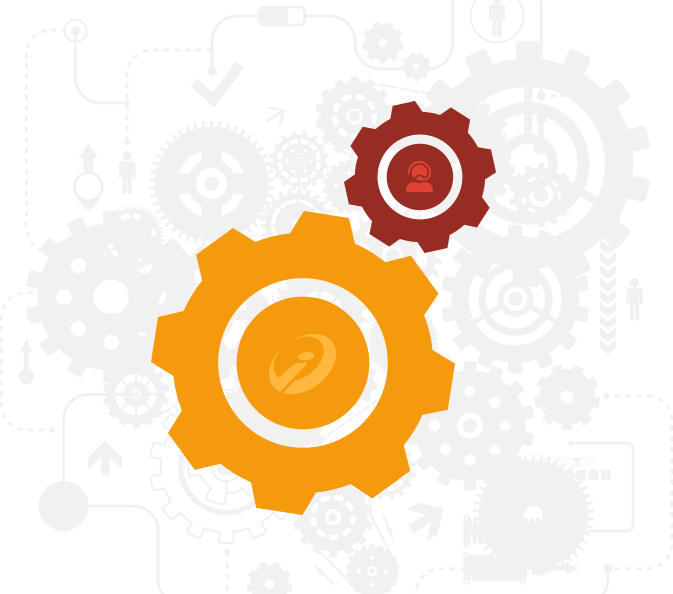
EDI is now process-related and sales-related
As group leader of the key account team, Alexandra Pitsch also looks after the EDI customers of MEYER-HOSEN AG. "A big advantage of i‑effect® is that all data transfers can be checked in one place," she says. "The frontend and the user experience are very good, you find your way around very quickly when it comes to integrating new requests in EDI business." In the past, she says, this was far too technical; today, the EDI infrastructure supports sales processes in a meaningful way.
Data exchange with the new solution
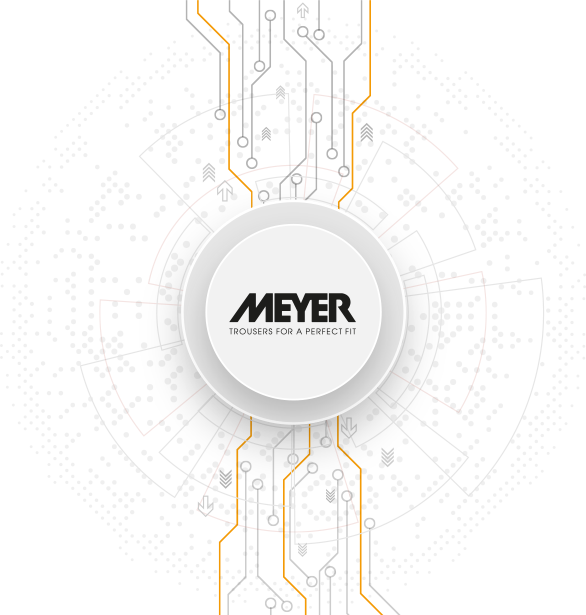
i‑effect® sorts XML streams generated by Infor-ERP according to defined criteria and converts them into the EDIFACT format required by the partner. Afterwards, the data is transferred via the preferred communication channel, usually via FTP or e-mail. For statistical purposes, the EDI platform fills a database for later evaluation by BI software. It retrieves incoming messages via e-mail or FTP and loads them from EDIFACT into Infor's in-house interface. i‑effect® maps all business processes. The textile manufacturer not only communicates with its trading partners via EDI, but also handles payment transactions with organizations such as the "BTE Handelsverband Textil". In addition, there is the electronic data exchange with end customers, because orders also come from them.
The XML data is provided via MEYER's online store and runs from there via i‑effect®'s mapping into Infor. Thus, goods movements and invoicing in the end customer business are also completely organized via the new EDI infrastructure, without the need for manual entry of order data - for the sales department, this means a great time saving and also minimization of errors that occur again and again due to accidentally incorrect entries. This cannot happen with automated processes. In the meantime, employees from IT and sales are well trained in using i‑effect® for their own research or for creating and updating master data. They can already carry out a large part of the adjustments themselves without having to rely on the help of menten support. And if support is ever needed: It is not far from Reichshof-Denklingen to Bergisch Gladbach, the headquarters of menten GmbH.
The company
Die MEYER-HOSEN AG mit Hauptsitz im nordrhein-westfälischen Reichshof-Denklingen ist ein führender europäischer Spezialist für nachhaltige Herrenhosen. Familiengeführt und regional verwurzelt im Bergischen Land, betreibt sie ein eigenes europäisches Produktionszentrum mit fairen und umweltfreundlichen Rahmenbedingungen. Von der Branchenzeitschrift „TextilWirtschaft“ wurde das Unternehmen als Top-Marke 2021 und für seine besondere Nachhaltigkeit ausgezeichnet.
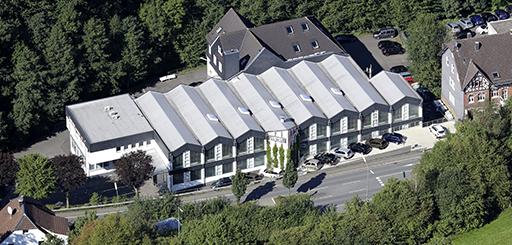
Challenges
MEYER-HOSEN AG is constantly striving to improve the technical aspects of EDI traffic with its trading partners - an important element in driving forward digitization within the company. However, this was no longer working well with the original solution: In 2007, the manufacturer had introduced a system that had not been technologically further developed in recent years - for MEYER in 2019, the reason to look for a modern alternative.
Solutions
They found menten GmbH as a recognized specialist for EDI and data conversion as well as data integration especially on IBM i and IBM Power Systems. Standard mappings were developed and these were adapted by menten after individual testing according to customer requirements. Conversions were made according to urgency and step-by-step according to format types. Master data and Excel lists from the previous tool were programmatically transferred to the new EDI platform i‑effect®.
Benefit
With its modular system, i‑effect® offers very high flexibility. MEYER-HOSEN AG can thus handle different business models via a uniform conversion and communication platform. A great advantage of i‑effect® is that all data transmissions can be checked in one place. Thus, goods movements and invoicing in the end customer business are completely organized via the new EDI infrastructure without the need for manual entry of order data - for the sales department, this means a great time saving and also minimization of errors.